Plastic molding is an important manufacturing process that allows for the creation of a wide range of products, from automotive parts to household items. Finding the right plastic molding machine is essential for factories providing OEM services to meet the diverse needs of various suppliers worldwide.
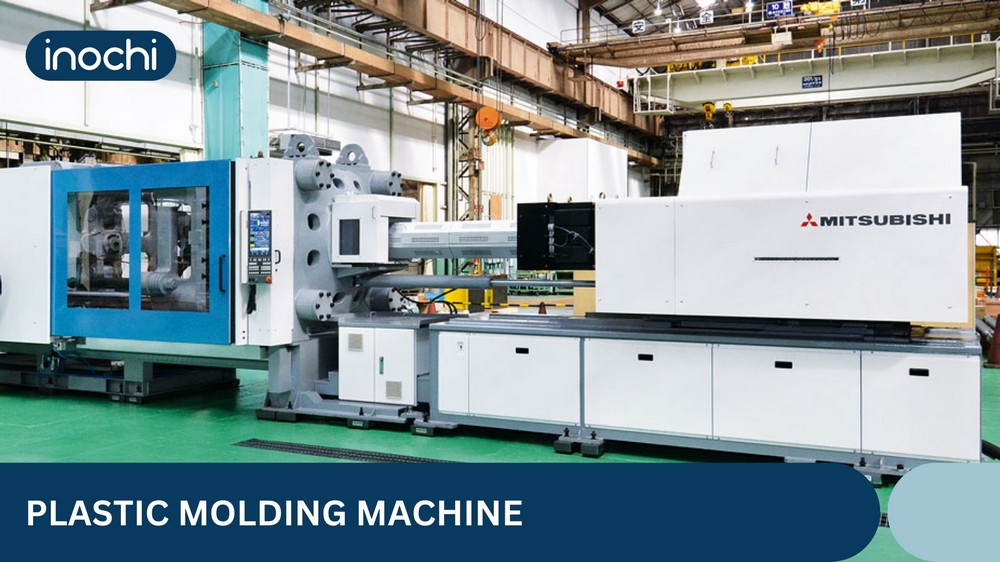
1. Top 3 Best Plastic Molding Machines
And here are the top 3 plastic molding machines from the three largest manufacturers in the world. Let’s take a look at their features below.
1.1. Haitian Mars Series – Haitian International Holdings Limited
The Haitian Mars Series is Haitian International’s best-selling line of injection molding machines. Some key strengths and features of this series include:
- High efficiency: The Mars Series machines are designed to be extremely energy-efficient, helping to reduce operating costs for customers.
- Precision and repeatability: The machines feature a new high-drive servo system developed by Haitian, which provides precise control and high repeat accuracy in the injection molding process.
- Intelligent controls: The Mars Series machines come with advanced software and control systems that enable open connectivity with smart manufacturing solutions.
- Wide application range: Available in clamping forces from 600 to 33,000 kN, the Mars Series can handle a diverse range of plastic parts, from consumer goods to large industrial components.
- Proven performance: With over 350,000 units sold, the Mars Series is the world’s best-selling injection plastic molding machine line.
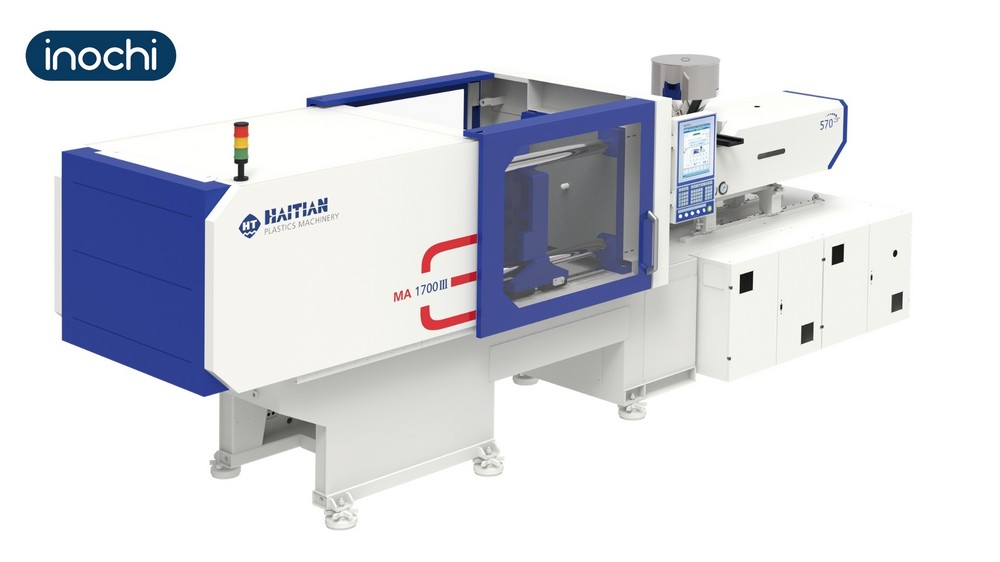
Other Key Product Series
In addition to the Mars Series, Haitian International offers several other advanced product lines:
- Jupiter Series: Haitian’s high-end two-platen machines, featuring ultra-large clamping forces up to 88,000 kN for producing giant plastic parts.
- Zhafir Electric Series: All-electric injection molding machines known for their energy efficiency, precision, and suitability for high-quality applications like optical components.
Global Presence and Support
Haitian International has established a strong global footprint to support its customers worldwide:
- The company has subsidiaries and technical centers in key markets like Japan, Vietnam, and Mexico to provide localized sales, service, and application support.
- Haitian’s global network of dealers and service centers ensures prompt access to spare parts and technical assistance for customers around the world.
- Regular open house events and factory tours at Haitian’s headquarters in Ningbo, China allow customers to experience the company’s latest technologies firsthand.
1.2. NEX-V Series – Nissei Plastic Industrial Co., Ltd.
The NEX-V Series is a Nissei Plastic Industrial Co., Ltd.’s new line of all-electric high-performance injection molding machine for plastic products. Here are the key details about the NEX-V Series:
- The NEX-V Series is designed to be Industry 4.0-ready, featuring the new TACT5 controller with OPC-UA communication protocol standard. This allows for integration with MES systems, mold-temperature-control systems, and hot runners.
- The series is available in clamping forces ranging from 30 to 360 metric tons, providing a wide range of machine sizes to suit different production needs.
- Despite the wide clamping force range, the NEX-V Series is designed to have one of the industry’s smallest footprints while maintaining large platen sizes and long daylights. This allows for greater flexibility in mold size and configuration.
- The machines are built to conform to the upcoming ISO20430 Universal Injection Molding Machine Safety Standard, ensuring high safety standards.
- Key features of the NEX-V Series include Nissei’s “N-Constellation” IoT technology for real-time data collection, remote monitoring, and predictive maintenance capabilities.
- The series is available in a range of screw diameters and injection capacities to handle a variety of part sizes and materials. The largest model, the NEX360V, can handle up to 982 cm³ of injection volume.
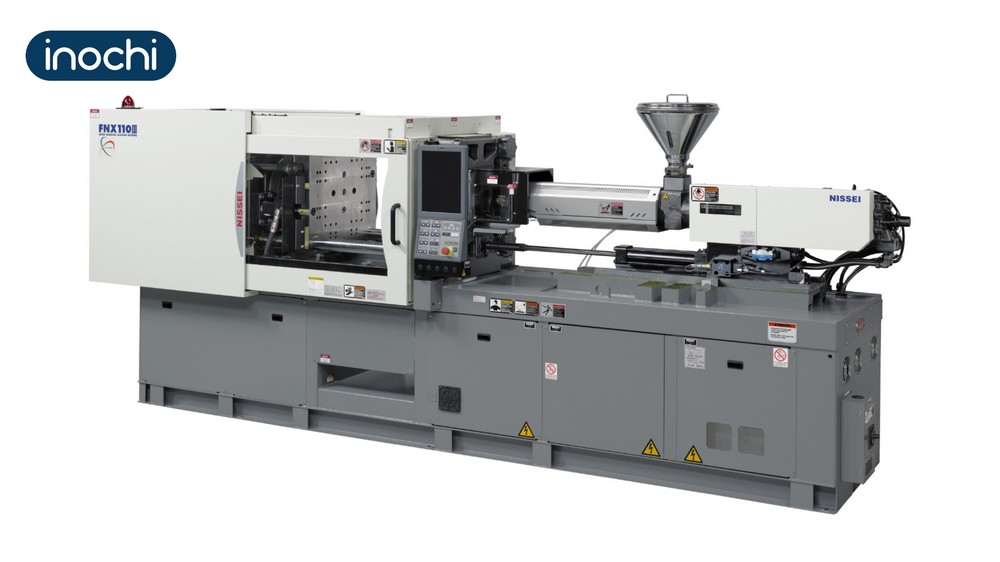
The NEX-V Series plastic molding machines can be used for a variety of applications, including containers, medical goods, and even molding of biodegradable materials like polyhydroxyalkanoates derived from corn or cassava. Isn’t that cool?
The machines can handle challenging molding tasks like preventing flash on difficult-to-mold materials.
1.3. ALLROUNDER Injection Molding Machines – Arburg GmbH + Co KG
Arburg is a leading manufacturer of plastic molding machines, and their ALLROUNDER series is a highly versatile and modular line of machines. The ALLROUNDER principle, developed by Arburg in 1961, features a pivoting clamping unit and interchangeable injection units, allowing for a wide range of applications and customization.
The ALLROUNDER machines come in hydraulic, hybrid, and electric variants, providing flexibility to meet different production requirements. They are available in a wide range of sizes to handle a variety of part sizes and volumes.
Some key benefits of the ALLROUNDER machines include:
- Adaptability: The modular design allows the machines to be easily expanded and configured to meet specific production needs. The swiveling clamping unit and reversible injection unit enable processing directly in the mold parting line.
- Versatility: Arburg offers a comprehensive range of ALLROUNDER models to handle a diverse set of injection molding processes and applications, from micro-molding to large-part production.
- Productivity: The machines can be equipped with Arburg’s servo hydraulic (ASH) technology or hydraulic accumulator options to enhance productivity and efficiency.
- Digitalization: Arburg integrates its ARBURG host computer system (ALS) and arburgXworld customer portal to enable Industry 4.0 connectivity and digital services for the ALLROUNDER machines.
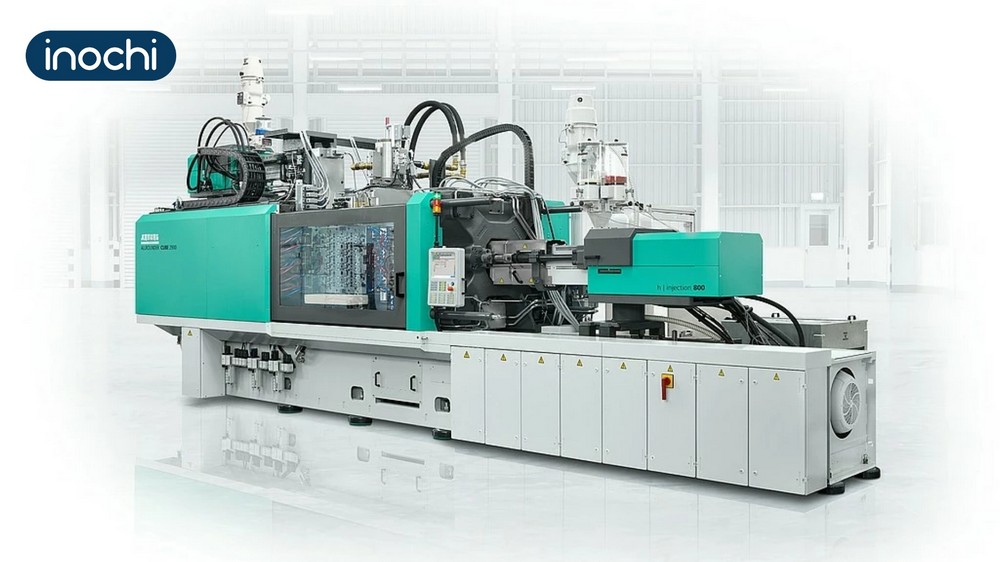
Arburg’s ALLROUNDER plastic molding machines are used across a wide range of industries, including packaging, automotive, medical, and consumer goods, to produce high-quality plastic parts. With their modular design, advanced technologies, and Arburg’s extensive expertise, the ALLROUNDER series provides tailored solutions for injection molding operations.
2. The Plastic Manufacturing Process of OEM Services
The plastic manufacturing process for OEM (Original Equipment Manufacturer) services typically includes the following main steps:
- Material Selection: Select thermoplastic or thermoset materials suitable based on the OEM’s requirements for properties such as mechanical, chemical, and thermal performance, as well as cost.
- Mold Design and Fabrication: Design and create molds using techniques like CNC machining or 3D printing to shape the plastic parts. This is a critical step.
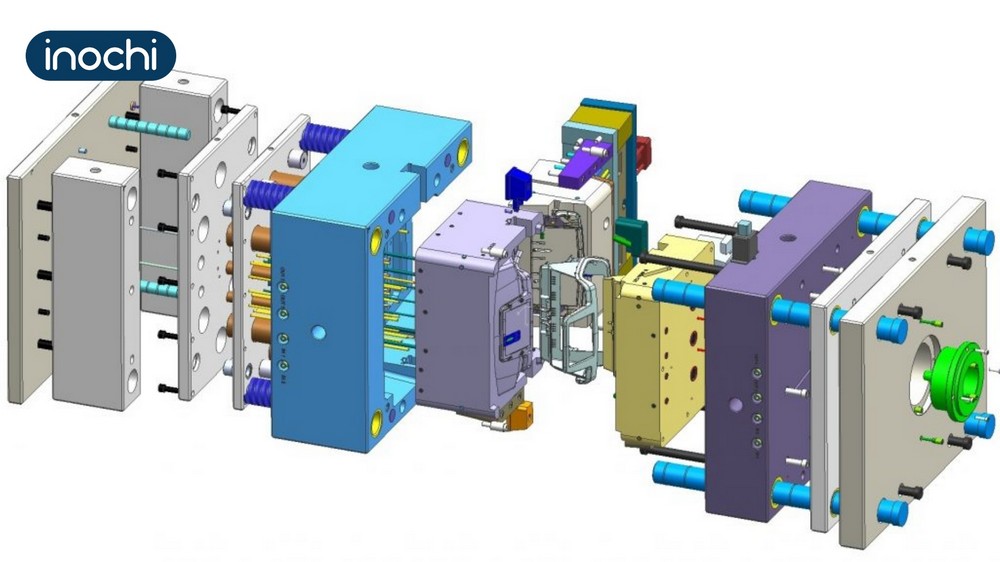
With Inochi Global, customers can fully request OEM services on our products, and there are two main types:
The customer brings the mold and Inochi manufactures according to the mold the customer has brought. And the second approach is that the customer will send the design to Inochi (both 2D and 3D), and then we will provide a quote for you as well as the estimated production time. It means that we can handle the entire manufacturing process, from design and engineering to production, assembly, and even packaging and logistics. For more information about Inochi Global’s OEM service, please contact us via Whatsapp: +84 85 555 5901. |
- Molding Process: Typically using injection molding, where molten plastic is injected into the mold cavity under high pressure. Other processes like blow molding or extrusion may also be used.
- Secondary Operations: Perform additional finishing, painting, or assembly when required to meet the OEM’s technical specifications.
- Quality Control: Implement rigorous testing and inspection procedures to ensure the parts comply with the OEM’s requirements.
- Packaging and Delivery: Carefully package the finished parts and ship them to the OEM customer.
The key benefits of OEM plastic manufacturing services include leveraging specialized equipment, expertise, and quality control to produce high-quality parts, and cost savings at scale for the OEM.
The above are the 3 best plastic molding machines from leading companies worldwide. These machines are of high quality, energy-efficient, and play a crucial role in OEM services for continuously producing quality parts. Distributors looking to enhance their brand visibility on products can collaborate with manufacturers for negotiations.